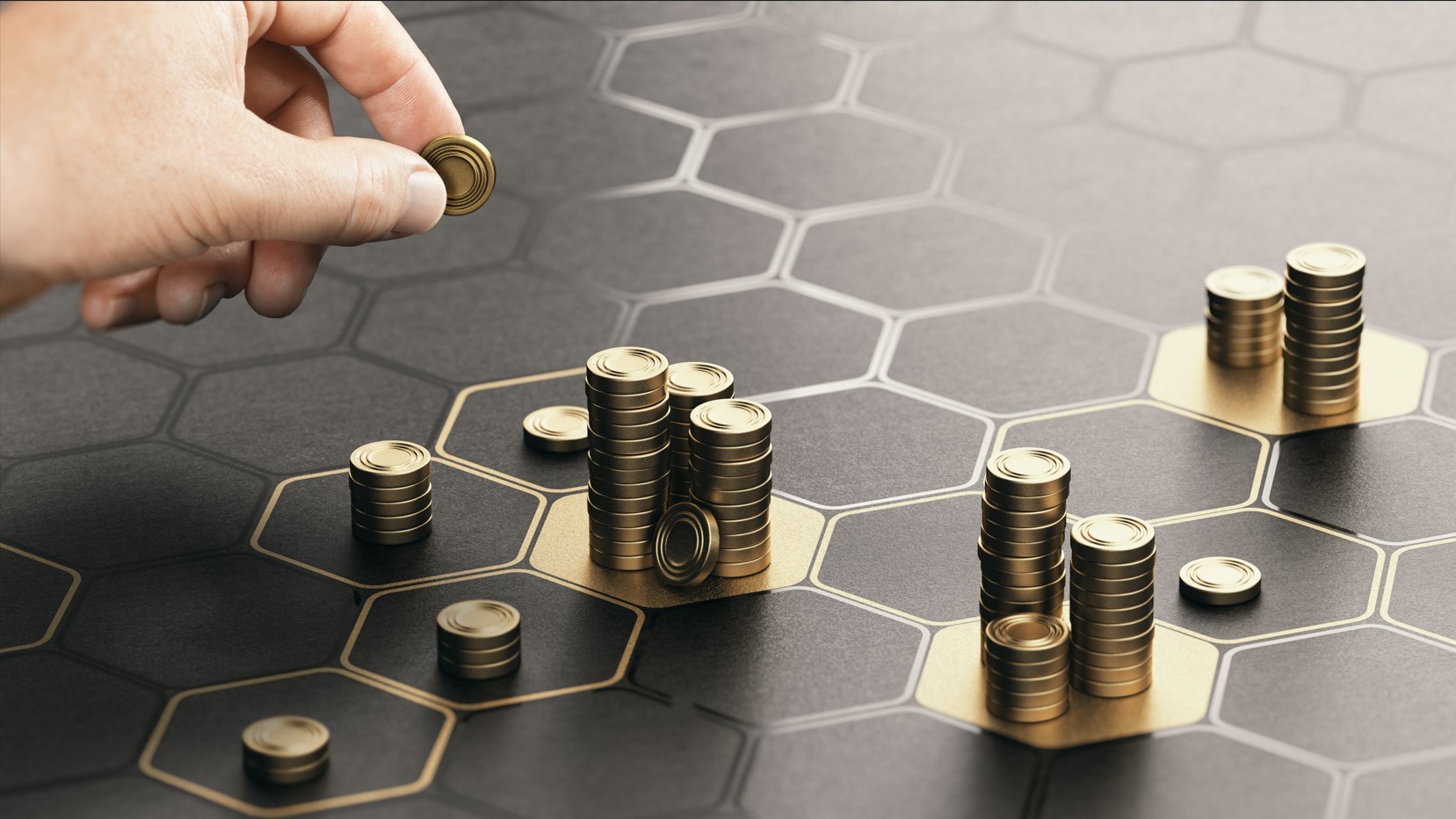
Industrial Parks Mexico
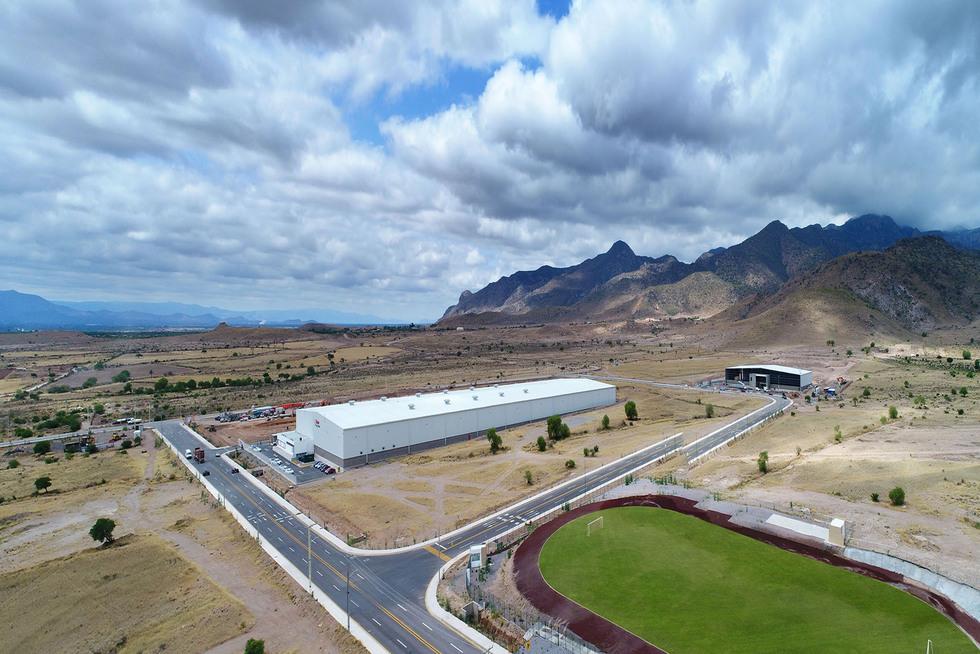
History of Industrial Parks in Mexico
The inception of industrial parks in Mexico is closely linked to the aftermath of World War II and the Bracero Program. With the program's conclusion, a surge of returning workers caused unemployment issues in northern Mexico. To address this, the Maquiladora Program (now IMMEX) was established, allowing tax-free import of raw materials for processing by U.S. companies operating in Mexico.
The demand for industrial spaces soared, particularly in border areas, leading to the creation of the first industrial parks. The Mexican Association of Industrial Parks (AMPIP) defines these parks as urbanized areas equipped with utilities, permits, and infrastructure for manufacturing and logistics. Today, Mexico boasts 368 industrial parks across 24 states, housing 3,417 companies, with 62% owned by foreign entities.
The organization Ampip
AMPIP advocates for best practices in industrial parks, emphasizing economic, social, and environmental performance. Various certifications, including Authorized Economic Operator (AEO), Safe Park, Green Park, and compliance with Mexico's Regulation for Industrial Parks, contribute to the competitiveness and sustainability of these parks.
Additionally, embracing Industry 4.0 trends, AMPIP promotes Smart Parks, encouraging innovation and technology adoption. Social Responsibility, Environment, and Governance Policies (ESG) are crucial considerations, reflecting a growing focus on long-term risk reduction and corporate value.
The evolution of industrial parks in Mexico is intricately tied to economic and historical factors. As these parks continue to grow and adapt, their adherence to best practices and certifications becomes imperative for fostering a sustainable and competitive industrial landscape.
High demand of Industrial Parks
Industrial parks in Mexico play a crucial role in attracting investments and fostering sustainable growth in the industrial sector. As of 2023, there are 425 industrial parks across 27 states in Mexico, according to data from the Mexican Association of Industrial Parks (AMPIP). It's important to note that AMPIP does not represent all industrial parks in the country, but it provides valuable insights into the industry.
The surge in the utilization of Mexico's industrial parks has been notable, especially with international companies shifting their supply chain operations to the country. This trend has been driven by the preference for industrial parks, which are reaching full capacity. In 2022, the nationwide availability rates dropped to 2.1%, indicating high demand. For example, in Monterrey, obtaining a lease often requires a 10-year commitment.
Approximately three-quarters of the occupants in these industrial parks are foreign companies, and according to a survey by BBVA bank, one in every five firms intending to establish a presence in Mexico is of Chinese origin, indicating a strategic move to navigate U.S. tariffs.
The nearshoring trend, where companies relocate part or all of their production to Mexico, has significantly impacted the demand for industrial spaces. The demand for nearshoring has led to the creation of jobs and increased foreign investment. While the construction of new industrial spaces has increased, there's still a need to meet the growing demand for investors requiring new productive spaces.
Who has the most industrial parks in Mexico?
The states with a significant number and quality of industrial parks include:
-Nuevo León: 80 industrial parks, mainly in the metropolitan area of Monterrey.
-Estado de México: 47 industrial developments, including parks, corridors, zones, and logistics developments.
-Guanajuato: 44 industrial parks.
-Coahuila: 34 industrial complexes.
-Chihuahua: 32 industrial warehouses.
-Jalisco: 25 industrial parks with both national and international companies.
The map shows all the Industrial Parks represented by AMPIP.
This graph shows the Tenants country of origin within AMPIP’s Industrial Parks, where the 62% are from another foreign country.
The impact of nearshoring is evident in the growth of foreign investment, especially from Asia. Chinese companies, in particular, have shown interest in Mexico, with 43% of companies interested in industrial spaces being from China.
As the demand for industrial spaces continues to grow, the construction of new industrial parks is expected to meet this demand. According to Claudia Esteves Cano, Director General of AMPIP, there are 50 new industrial parks in different stages of development in Mexico, with some expected to start operating in 2023 and others gradually becoming operational until 2025.
The stages of development for industrial parks include:
-Land Acquisition: The park has the land, and processes are underway to initiate construction.
-Permitting: The park is obtaining all necessary permits from authorities for infrastructure development and service feasibility.
-Infrastructure Development: The park is developing infrastructure such as roads, booths, and services on the lots.
-Occupancy: The park is taking actions to attract the first company for installation.
The classification of industrial parks based on their development stages, perimeter, and purpose provides a comprehensive understanding of their diversity.These classifications include:
-Development of Infrastructure: Parks in construction (10%).
-Perimeter: Closed parks (68%) with complete delimitation and controlled access, and open parks (32%) with monitored access points.
-Purpose: Manufacturing (12%), Logistics (12%), Mixed-use (75%), and Dedicated (1%).
The dynamism in the industry is reflected in the sectors with the highest activity, including Manufacturing (54%), Automotive (18%), Logistics (17%), High-Tech (3%), and Others (8%). The markets with the highest activity are in the North (41%), Bajío - Occidente (30%), and Mexico City and Metropolitan Area (17%).
Looking ahead, the publication of the Law of Quality Infrastructure is expected to establish norms and standards related to the Mexican Industrial Park Standard, defining criteria for what qualifies as an industrial park and establishing minimum and maximum requirements.
Classification of Industrial Buildings
In Mexico, numerous industrial parks, encompassing millions of square feet, play a pivotal role in fostering economic activities. The majority of these parks are situated within gated environments, ensuring security, while others comprise standalone buildings with their own security measures. These industrial spaces fall into distinct categories, aligning with the guidelines established by NAIOP, which classifies them as Class A, Class B, and Class C buildings.
NAIOP Classification of Industrial Buildings
Class A Buildings: Representing the pinnacle of quality and innovation, Class A buildings are the newest and boast the highest standards in the market. Their building systems, including mechanical, HVAC, elevators, and utilities, meet both current tenant requirements and anticipated future needs. These buildings feature above-average maintenance, management, and upkeep, making them ideal for high-quality tenants. Notably, a Class A building may exhibit some, but not necessarily all, of these characteristics.
Class B Buildings: Slightly older than Class A, Class B buildings feature quality management and are recommended for processes such as casting, forging, and machining. With minimal improvements and renovations, Class B buildings have the potential to return to Class A status. Their building systems have adequate capacities to meet current tenant needs, with maintenance, management, and upkeep characterized as average to good.
Class C Buildings: Class C buildings are older structures that often require major improvements. Despite their age, they remain functional and structurally sound. The building systems may have capacities that do not fully meet current tenant needs. Maintenance, management, and upkeep are below average, and these buildings typically rely on competitive pricing to attract tenants.
Under-Roof Industrial Space in Mexico:
Water service, sanitary facilities, sewer systems, natural gas, electricity, and communications are generally readily available in Mexican industrial parks. Additionally, these parks can accommodate additional utilities required by businesses, such as HVAC, FM-approved fire protection systems, and mechanical systems. Companies leasing vacant buildings within these parks may need to contract for these services, and both industrial parks and shelter companies play a vital role in facilitating the establishment and ongoing management of these services.
Security Measures and Minimum Requirements in Mexican Industrial Parks
The establishment of industrial parks in Mexico has been on the rise, driven by the demand from both national and foreign companies. According to the analysis by the AMPIP (Mexican Association of Private Industrial Parks), the main causes include the reorganization of the supply chain, the strength of the U.S. economy, the consequences of the USMCA (United States-Mexico-Canada Agreement), the well-known trade war between the United States and China, and the conflict between Russia and Ukraine.
These circumstances have compelled companies to seek new replenishment centers, coupled with changes in consumer habits post-COVID-19. Approximately 47 new industrial parks are expected to enter the market this year, with an investment of $1.8 billion, projecting an annual growth of 10-15% in the industrial furniture business for at least the next four years.
The automotive industry is a major demand driver for these spaces, with significant investments observed in industrial parks in Tijuana, Chihuahua (Cd.Juárez), Saltillo, Querétaro, San Luis Potosí, Monterrey, Aguascalientes, Tamaulipas, Puebla, Jalisco, and the State of Mexico.However, some of these areas, particularly Puebla, Jalisco, and the State of Mexico, are also affected by monthly cargo transport thefts and, in some cases, organized crime.
To understand the challenges and ensure the security of these crucial industrial sectors, experts highlight several security threats, including armed personnel intrusion for product theft, unauthorized access, and disruptions in operations. Different industrial parks face varying risks based on geographical regions, types of operations, and the nature of the industries involved.
Main Security Threats
-Armed Intrusion for Theft: Armed personnel intrusions for product theft, unfortunately, occur frequently in countries like Mexico, Brazil, and Chile. The main risks involve massive product loss, collateral damage such as loss of lives or injuries.
-Unauthorized Access: The first security ring of the park is crucial, and if violated, intrusion can lead to various issues such as aggression and theft. The impact on operations is significant, affecting commitments with clients and suppliers, as well as logistics.
-Operation Blockage: Blocking operations has a substantial impact, affecting commitments with clients and suppliers and disrupting overall logistics.
Risk Assessment and Mitigation:
Risk assessment methodologies, including checklists, fault tree analysis, hazard and operability analysis (HAZOP), cause-effect analysis, and risk treatment proposals, help identify, classify, and prioritize risks. Once classified by impact and probability, action plans are established to influence the likelihood and impacts on the organization.
Physical Security and Technology
-Perimeter Security: A solid perimeter, difficult to access, with appropriate height, barbed wire, or concertina, surveillance cameras, sensors, and adequate lighting are essential. Regular patrols, maintenance checks, and audits validate the effectiveness of security measures.
-Technology Integration: Beyond private security, technology plays a crucial role. Access control measures, pre-registration of individuals and vehicles, documentation checks, and technologies such as cameras contribute to a layered security approach.
-Video Surveillance: A robust video surveillance system is recommended, capable of detecting abnormal behaviors, monitoring external incidents, and serving as evidence in case of events. Adequate advisory support ensures that the installed system achieves its protection goals.
-Crime Prevention Through Environmental Design (CPTED): Implementing CPTED, a multidisciplinary approach to prevent crime through urban design and architecture, helps deter criminal activities, foster community engagement, and reduce overall crime.
Security of Personnel:
-Internal Security Culture: Fostering a safety culture among park employees through continuous awareness, training, and the creation of emergency response protocols contributes to a safer working environment.
-Autoprotection Training: Employees should receive training on self-protection, understanding risks, and knowing what actions to take in case of major events. Avoiding concentration of power in a single employee and implementing proper segregation of duties enhances safety.
Protection of Goods and Merchandise:
-Warehouse Security: Individual tenants are responsible for warehouse security. Effective communication between the park control room and individual warehouse control rooms is vital. Patrolling, high-definition cameras, and counter-surveillance outside the park contribute to overall security.
-Material Handling and Employee Training: Paying attention to scrap or waste management, employee training on proper tool and inventory handling, and conducting random inspections are critical measures.
Fire and Explosion Preparedness:
-Emergency Protocols: Protocols for incidents like fires or explosions should be well-documented and communicated to all areas. Simulations, at least every six months, involving a Mutual Assistance Committee, ensure readiness and coordination with relevant authorities.
Prevention in Calm Times: During calm periods, focus on developing and implementing safety policies, creating a prevention culture, disseminating information, and conducting integrated risk analysis.
Sustainable Parks
Sustainable industrial parks in Mexico are gaining prominence as businesses increasingly prioritize environmental, social, and governance (ESG) criteria. These criteria play a crucial role in attracting investments and accessing attractive sources of financing.
The concept of sustainability has evolved since the Rio Summit in 1992, leading to the adoption of the 2030 Agenda and its Sustainable Development Goals (SDGs) by 193 UN member countries in 2015. These goals emphasize the interconnected dimensions of social, economic, and environmental development, calling for collective efforts from all stakeholders.
In Mexico, the Mexican Association of Industrial Parks (AMPIP) has been proactive in incorporating sustainability criteria into the design and operation of industrial parks. The Mexican Regulation for Industrial Parks (NMX-R-046-SCFI-2015) has included sustainability criteria for several years. Many industrial parks in the country have undertaken initiatives to achieve certifications for sustainable building, implement efficient water and energy usage mechanisms, and establish policies for waste reduction.
AMPIP actively fosters the exchange of experiences and best practices, addressing environmental risks, and aligning with global trends in innovation and sustainable infrastructure.
The analysis of sustainable commitments among AMPIP industrial parks reveals a growing trend in the adoption of measures related to sustainability, with nearly 70% of the member parks actively monitoring sustainability issues within their operations.
Several sustainability certifications are prevalent among AMPIP members, including LEED (Leadership in Energy & Environmental Design), EDGE (Excellence in Design for Greater Efficiencies), GRI (Global Reporting Initiative), and GRESB (Global Estate Sustainability Benchmark).
In 2022, AMPIP joined the United Nations Global Compact, reinforcing its commitment to integrating the Compact's Ten Principles on human rights, labor rights, the environment, and the fight against corruption into the association's culture and strategy.
The commitment to sustainability extends beyond the physical infrastructure of industrial parks. Developers are incorporating technology and innovation into the design of industrial spaces, embracing concepts like Building Information Modeling (BIM) to generate and manage building data throughout their life cycle.
Furthermore, industrial parks are designed to enhance the quality of life for workers, incorporating amenities such as daycare facilities, sports courts, and common recreational areas. In terms of security, companies within global supply chains often seek certifications such as the Operador Económico Autorizado (OEA) in Mexico and the Custom Trade Partnership Against Terrorism (C-TPAT) in the United States.
The logistics sector dominates the portfolio of industrial real estate, aligning with the rapid growth of e-commerce. Mexico ranks ninth globally and first in Latin America in the Logistics Performance Index. The demand for logistics spaces accounted for 34% of total industrial space demand in 2021, emphasizing the strategic location of industrial parks near major trade and distribution routes.
As logistics undergoes constant transformation, automated supply chains leveraging technologies like the Internet of Things, automation, big data, and cybersecurity are becoming more prevalent. Industrial developers are adapting to these trends, incorporating processes to identify and mitigate potential risks and vulnerabilities in line with international standards for physical, information, and process security applicable to industrial parks.
In the context of the fourth industrial revolution (Industry 4.0), developers are constructing spaces that integrate technology and innovation, addressing the needs of companies engaged in the widespread use of disruptive dynamics such as augmented reality, additive manufacturing, robots, and cloud computing.
The rise of sustainable industrial parks in Mexico reflects a global shift towards environmentally responsible and socially conscious business practices. The commitment to sustainability not only aligns with global goals but also positions Mexico as a destination for companies seeking eco-friendly spaces and investors looking to support environmentally responsible ventures.
Chen, J. (2022). Industrial Areas: Overview, Significance, Special Considerations. Retrieved from https://www.investopedia.com/terms/i/industrial-park.asp
Acosta, M. G. (2023). How many industrial parks exists in Mexico? Retrieved from LinkedIn: https://www.linkedin.com/posts/mgaytan1_cushwakemx-strategicconsulting-industrialbroker-activity-7123350257765134336-cWo-/
Advance Real Estate. (2022). ¿CÓMO TENER UN PARQUE INDUSTRIAL SEGURO? Retrieved from https://advance-realestate.com/adblog/como-tener-un-parque-industrial-seguro/
Animal Político. (2022). La importancia de la sostenibilidad para el desarrollo de los parques industriales.Retrieved from https://www.animalpolitico.com/hablemos-de/sustentabilidad/importancia-sostenibilidad-parques-industriales
Gurrola, K. S. (2023). INDUSTRIAL PARKS IN MEXICO History and Best Practices Based on Certifications. Retrieved from https://www.airealestate.com.mx/en/blog/industrial-parks-mexico-history-best-practices-based-certifications/
Industrial Plot. (2021). What are the Different Classes of Industrial Buildings? Retrieved from https://industrialplot.com/what-are-the-different-classes-of-industrial-buildings/
Juárez, C. (2023). Parques industriales en México: ¿en dónde se encuentran?Retrieved from https://thelogisticsworld.com/logistica-y-distribucion/parques-industriales-en-mexico-en-donde-se-encuentran/
Martínez, C. (2023). Parques industriales en México: clasificación, etapas de desarrollo y demanda frente al nearshoring.Retrieved from https://thelogisticsworld.com/logistica-y-distribucion/parques-industriales-en-mexico-clasificacion-etapas-de-desarrollo-y-demanda-frente-al-nearshoring/
Ramos, M. (2023). SEGURIDAD EN PARQUES INDUSTRIALES.Retrieved from https://www.seguridadenamerica.com.mx/33912/seguridad-en-parques-industriales-1
Rangel, J. (2022). Sustentabilidad, tendencia para la construcción de parques industriales.Retrieved from https://inmobiliare.com/sustentabilidad-tendencia-para-la-construccion-de-parques-industriales/